Machining Projects
Spring 2022 - Present
These are just a few of the parts that I have machined since I learned about subtractive manufacturing. I've come really enjoy working with manual machines, and hope to engage in more small projects for myself. Learning how parts are actually made has become so crucial to my ability to design for manufacturing! If you have any cool ideas for things to machine, send them my way so I can give them a shot!
​

Mechanical Technology Sequence
The following projects were developed in the Mechanical Technology course sequence at Brown University. The majority of projects were completed on reliable Bridgewater lathes and mills. These machining projects provided me with a deeper understanding of how parts are made. Moreover, I learned to carefully consider the engineering design process and to always design for manufacturability. I am thankful for the opportunity to participate in this competitive in-depth course that has fostered a new passion for machining.
Spring-loaded Tap Center
​The first project in the sequence consisted of a quick introduction to the lathe. Stock cold-rolled steel was prepared in a vertical bandsaw and faced off on the lathe. This project consisted of the operations like turning, drilling, and tapping. Tolerances were slim on the order of 3-5 thousandths as the inner piece needed to fit flush into the outer cylinder. The spring-loaded tap project took approximately 6 hours to complete.

Mallet
The mallet, also manufactured from cold-rolled steel, consisted of operations on a mill and lathe. On the lathe, the stock was faced off, drilled, tapped, and bored. The mill was used to drill a hole through the head to push a pin through the shaft. Lastly, the head and shaft were pressed into the provided handle, and a pin was pushed in to secure it. This project took about 12 hours in total to complete

Parallel Clamp
The parallel-clamp project used a cold-rolled steel stock material and utilized a combination of a mill, lathe, bandsaw, and metal bending brake. The rods were turned on a lathe, and the gripping heads were knurled using a knurling tool. The rods were then threaded manually on a lathe. The clamp heads were cut on a bandsaw and milled carefully to accommodate for the rods. The stopping clip was cut, milled, and bent. This project took about 18 hours in the shop to complete.

Tapping Block
​The tapping block project used cold-rolled steel stock material. A triangular lathe chuck was used to drill out the center of the block. A reamer was used to ensure the dimension of the hole was accurate. The mill was used to drill the surrounding holes, which were then reamed as well. This project took about 4 hours total to complete.

Formula SAE Projects
This past Spring of 2023, I was asked to assist Brown's formula team in a couple of last-minute tasks before the competition in May. Due to a heavy courseload and leadership positions with Brown Space Engineering, I haven't had much time to engage with the Car Team, but I am thankful for the opportunity to contribute to this year's car. I hope to contribute more to the car in the fall, as a new aerodynamics subdivision is being added for the project.
Suspension System Spacers
While this is a smaller project, it was my first with the Formula team. Due to a tolerancing issue on the chassis, custom-made spacers were needed to ensure there was no wiggle room for the bolts that connect this suspension beam to the chassis. To fix this issue, I measured the actual hole and the space between the holes to develop a rough sketch of the design I had in mind. Knowing I needed to secure a 1/4-20 screw, I grabbed cylindrical stock and took it to the lathe to turn these spacers. Since I needed to make four of them, I came up with a method to streamline the process, performing the same operation for each component at the same time rather than doing one component at a time. Considering the tight tolerances here, I used micrometers to ensure I was getting a tight fit on the car. This mini project was a success, and my parts were used in the competition in the race. I look forward to contributing more to the car in the fall!
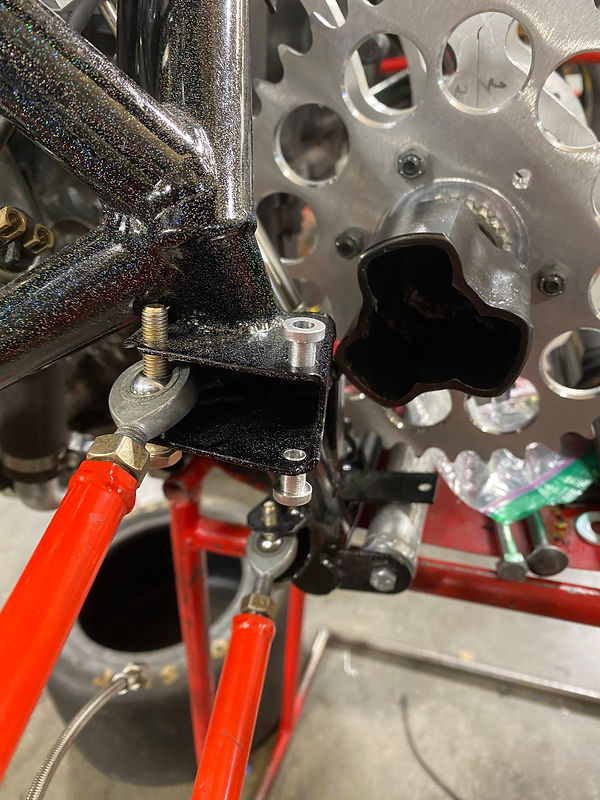